During the last week or so, I’ve been mulling over what to do with all the metal goodies
I have. If you don’t remember, this is the pile.
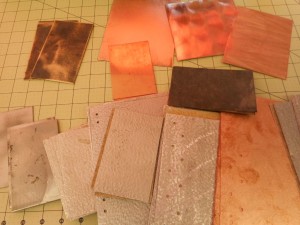
I’m concerned about adhering anything, leather, cloth, tapes, etc., to the metal as it will need a strong bonding agent. The ability of any material to withstand constant contact with metal may be another problem. For example, in a Coptic binding, how quickly will the metal cut through the binding thread? I’ve smoothed and rounded the edges and corners, but will it be enough? Will I have to cover the edges with a softer material? So far lots of questions, no answers. This is what I have planned out, now to try to find out what will work.
-
-
Leather-bound book with copper plate
-
-
-
Marbled endpapers
-
-
Completed book
-
-
Small notepad holder
-
-
Interior
-
-
Interior
These two have already been finished. The book cover was made by creating a “sandwich” of two pieces of binders’ board with the copper plate in the middle. The center of the top board was cut out, exposing the copper. This is one of the easiest and most secure methods of using metal, but it is essentially just decorative, not an integral part of the structure of the book. For the small notepad, I glued the metal directly to the leather spine using a metal adhesive. There were remnants of adhesive webbing on the reverse of this aluminium, so I just used PVA on the marbled paper. This is a prototype and it will take some testing in use to see if the leather needs reinforcing or if other adhesives are needed. I decided to do this one as simply as possible to test the strength of the bonding.
Now for what’s in planning stages:
-
-
Brass Plate for Book
-
-
Pages
-
-
Pages & endpapers
-
-
Brass Plate for Box
These two lovely brass plates were originally intended to be front and back covers, but while playing, I changed my mind. I tried them with a dark brown leather, but much preferred the look against a black Italian bookcloth. Sam Castner textured these for me and I really like the edges, so instead of making a sandwich as I did for the copper, I’m going to inset one into a book cover. To inset, I’ll carve a piece out of the top board just slightly larger than the brass. The boards are then covered with bookcloth, which is pressed into the depression, and the brass is adhered as the final step. The green decorative paper will be used for endpapers and the lacy tissue makes section dividers. The other brass piece will be inset into a clamshell box that will be made to fit the finished book.
-
-
Aluminium Covers
-
-
Covers, pages and endpapers
-
-
Endpapers
-
-
Book before sewing
Although I don’t care for Coptic bindings in general, I thought I would try at least one and the holes were punched on these plates for Coptic sewing. I’ve added a leather lacing just for decoration. I’m going to sew this with a heavy waxed thread, but really expect the metal to cut through it. It’s worth trying on a prototype anyway. Sewing on cords that are laced into the cover will probably be a better technique.
-
-
Copper plate with great texturing
-
-
Holes for lacing with round leather
-
-
Laced rawhide strap on copper
-
-
Brown leather, perhaps for spine
I’m completely undecided about this last piece. I love the copper plates and want to use them as the boards for a book, but I have no clue as to how I’ll construct the spine. At the moment, I’m thinking about a leather covering over wrapped cords. Maybe using rawhide or leather thongs for the cords and lacing them into the copper. The holes in the copper can be used structurally or just for decoration. They could be covered with leather or bookcloth or left exposed. Not sure of anything, just know I love this copper and will have to find an appropriate venue for it.
Like this:
Like Loading...